大西工場内をご案内します!
好きなポイントをクリックしてください。
●赤いポイント は動画になっています。音も出ますのでご注意ください。
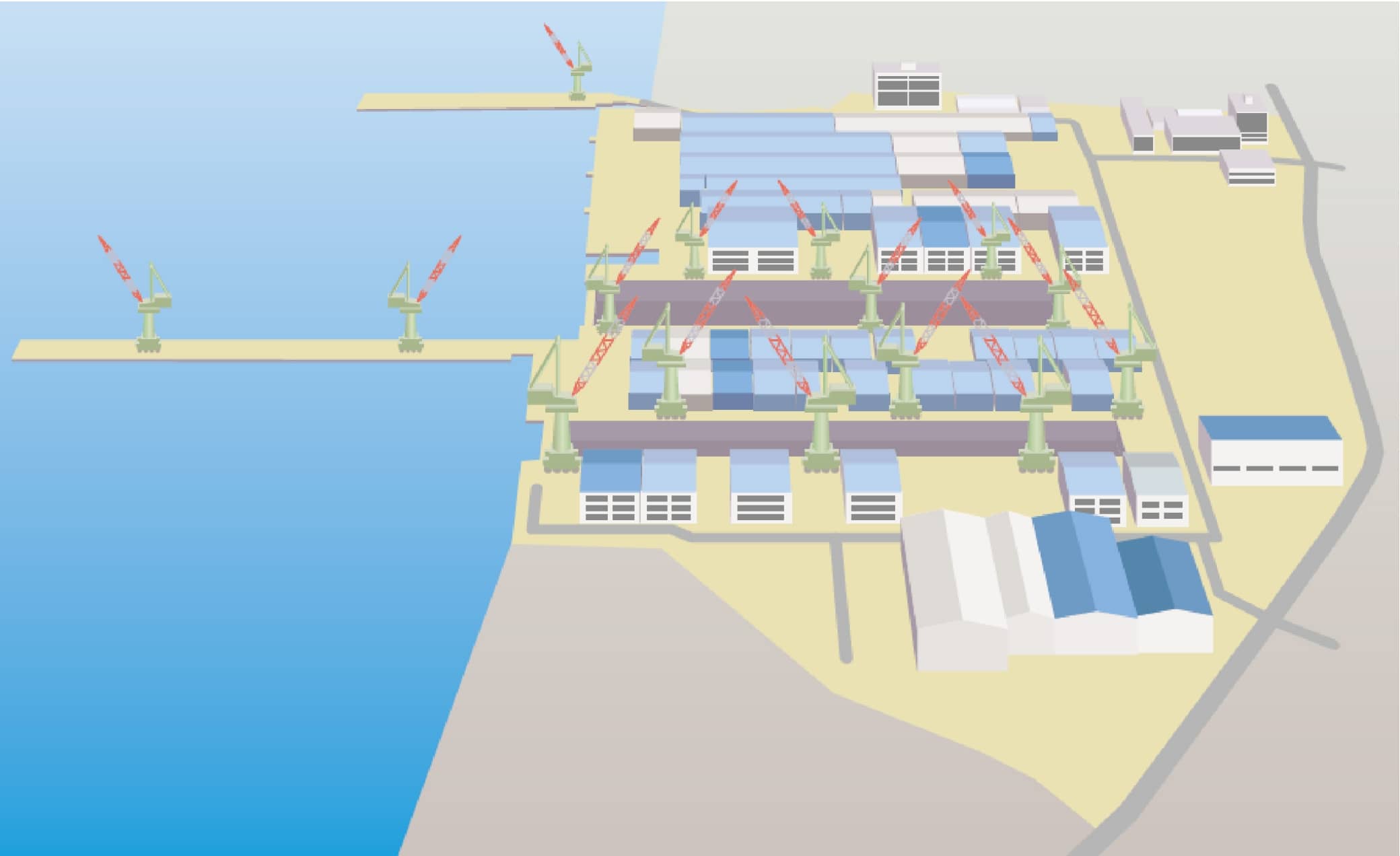
新来島どっく大西工場
大西工場内をご案内します!
好きなポイントをクリックしてください。
●赤いポイント は動画になっています。音も出ますのでご注意ください。
新来島どっく大西工場
3000Tプレス
3000Tの圧力をかけて、金型を押し当ててプレス曲げを行います。16m×4.5mもの大きな鋼板を曲げます。
主にステレンスケミカルタンカーのコルゲート(隔壁)や曲げが必要な大型部材を一日に5~6枚曲げています。
NC切断
設計データに基づき、鉄板を自動切断します。大西工場には、計11台あり、朝から夜中まで稼働しています。
ぎょう鉄
船体の複雑な曲がり部分は、人の手によって鉄を熱して、冷やしてを繰り返して、曲げていきます。
マニュアルも手順書も無い、まさに「匠の技」の世界です。
総組立
ドックにクレーンでブロックを搭載する前に地上で可能な限りブロックを繋ぎ合わせておきます。
ドック内では、高所で上向き作業となることが多く、作業効率が悪くなりますので、安全性と作業効率の高い地上で出来ることを行います。
艤装岸壁
船体を浮かべた後も船はまだ作業が多く残っています。船員が生活する居住するエリアの内装や配線を行います。また船に取り付けられた各装置が問題なく動くか、テストが行われます。この艤装工事がすべて完了すると、実際に船を走らせて、スピードやバランステストを行い、きとんと仕様書通り、性能を有しているか確認を行います。
水切りヤード
造船所の入り口。製鉄所から輸送される鉄板は、ほぼすべてここで入荷されます。
一日に100T以上もの鉄板を入荷しています。
建造ドック
地上で総組立を行ったブロックは、ドック内へ搭載されていき、段々と船のカタチになっていきます。
すべてのブロックが搭載され溶接や塗装が完了すると、いよいよ進水となります。
大西工場には3本の建造ドックがあり、それぞれのドックで色々な船を同時並行で建造しています。
大組立
鉄板の加工が終わった後は、鉄板同士を溶接して繋ぎ合わせていきます。
小さな部品を組み立てる「小組立」、さらに小組立で出来た部品同士を組み立てる「中組立、大組立」と段々とブロックと呼ばれるものになっていきます。
この段階でも溶接不良や精度不良が無いか細かくチェックを行います。
※写真は360度スクロールしてご覧いただけます。
先行艤装
船体ブロックへのパイプの取り付けや航行装置を取り付ける作業を艤装と言いますが、できるだけ地上のブロック段階で終わらせるよう、取り組んでいます。取り組むことにより、工期の短縮化、作業効率、安全性の向上が期待できます。
管工場(パイプ製作場)
船の血管とも言われるパイプの製作を行っています。大西工場の管工場(パイプ製作場)は、大西工場、波止浜どっく、広島どっくで建造する船のパイプをすべて製作しています。
工場内は、パイプの口径別に製作ラインが分かれており、自動化が進んでいます。
製作本数は、造る船の種類によって、左右されますが、月に約20,000本です。
塗装
船体の塗装は、ブロック段階で錆落としを行った後、数回、塗装を行います。塗装が脆いと船体の腐食が広がりやすく、航海中の事故に繋がりかねません。
塗装工場内は、除湿器を設置し、湿度管理を細かく行っております。
ラインウェルダー
造船に使用する鋼板には強度部材としてロンジというパーツを取り付けます。
自動ロンジ溶接装置「ラインウェルダー」を使用し、同時溶接を行なっています。